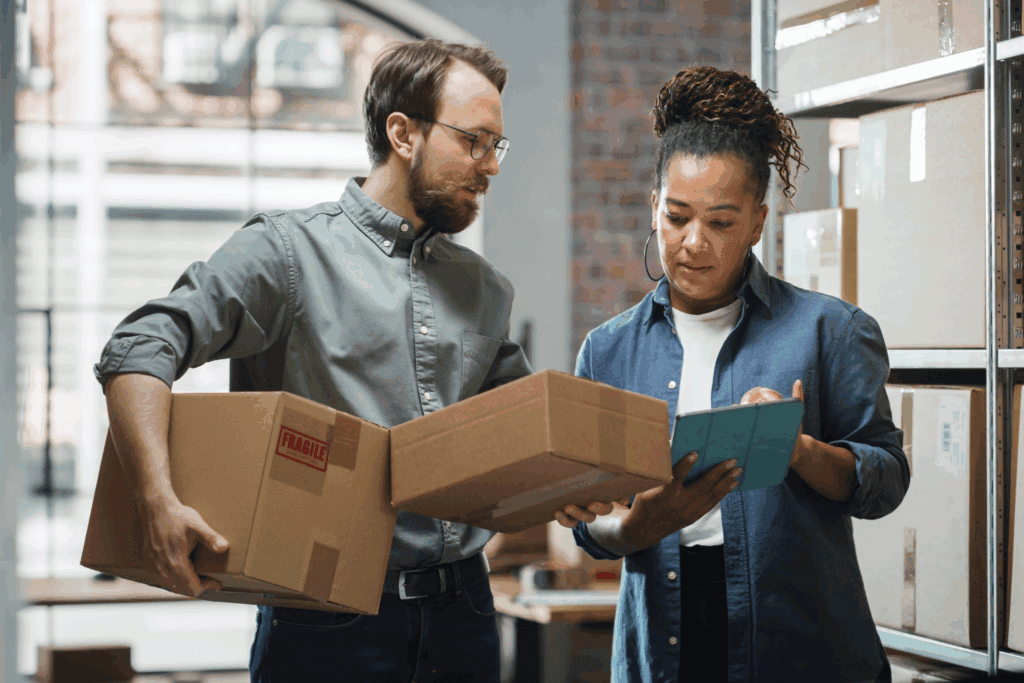
Small Business Essentials: Understanding The Four Types Of Inventory
Let’s be honest: You might not love dealing with inventory, but mastering it can make all the difference between a successful business and an out-of-control one. Whether you’re running a bustling retail shop, a cozy café, or a neighborhood liquor store, you likely have multiple different types of inventory working together at once.
Here’s the good news: Once you know the four types of inventory, you can spot problems, save money, and keep your customers happy. As inventory management pros, we’re here to demystify the four types of inventory every small business owner should know.
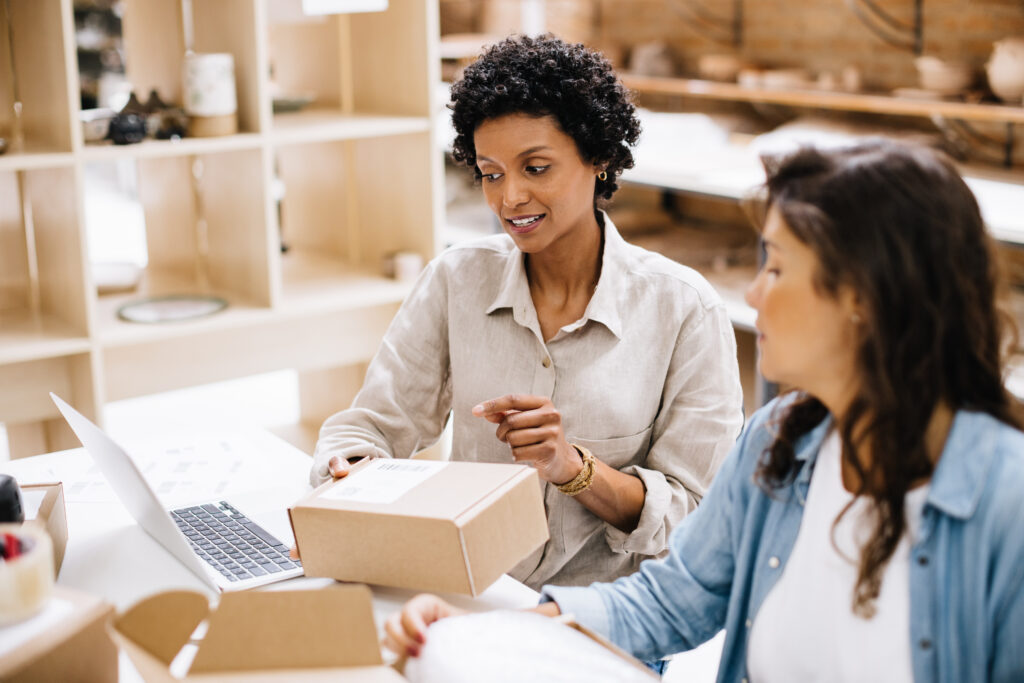
Why It’s Important To Understand The Four Different Types Of Inventory?
Knowing the different types of inventory is like having a roadmap to better back-office operations. It helps you see where your money is tied up, where improvements can be made, and how to keep your business running smoothly and profitably.
- Improve inventory management: Avoid confusion when you’re trying to craft a product or fulfill an order with complete visibility and control over every part of your inventory.
- Reduce waste and shrinkage: Identify slow-moving or obsolete items early to minimize losses, retain profit, and free up valuable space.
- Optimize cash flow: Better understand how much your products really cost so you can make more informed purchasing and pricing decisions.
- Meet customer demand: Ensure you have the right products available when customers want them, with accurate inventory counts.
Power Up
Just getting started with inventory management? Discover all the ins and outs with our Complete Guide To Inventory Management.
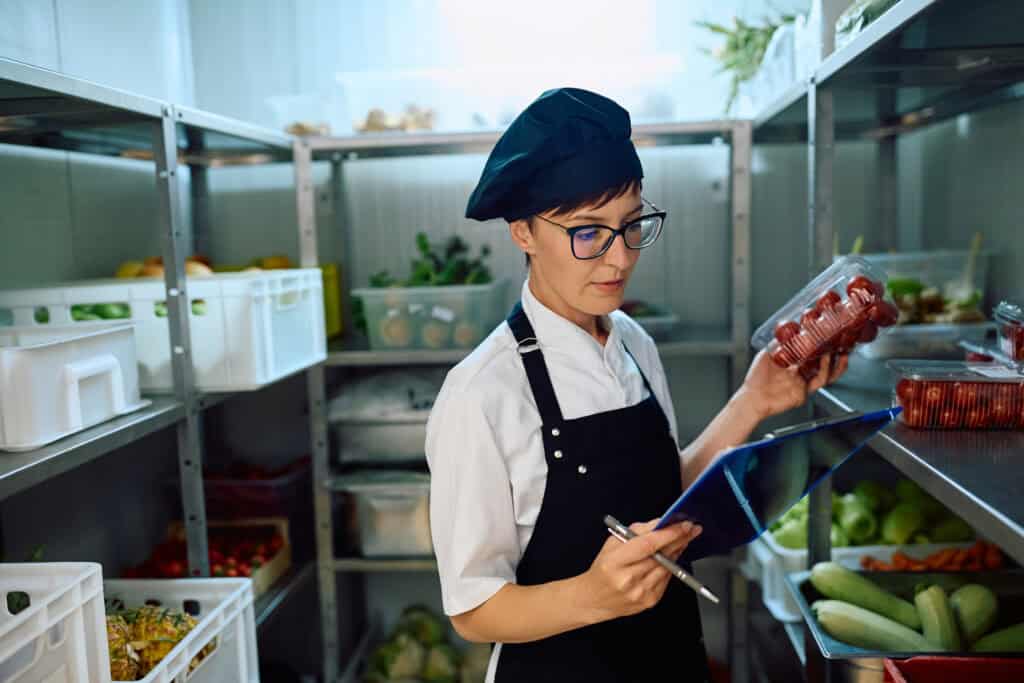
Definitions And Examples For Each Inventory Type
Raw materials
If you make, craft, or customize your products, raw materials are the foundation of your production process. These inventory components are the essential building blocks that transform into the products your customers love.
Examples of raw material inventory
- Flour, eggs, and vanilla extract that get baked into a cake
- Thread that you customize monogrammed pillowcases with
- Wax, essential oils, and glass containers for pouring handmade candles
Raw materials are typically categorized with an “unfinished” status, however, they are an important part of inventory management. By understanding how to track and optimize your raw materials, you:
- Have the right materials on hand, preventing costly production delays and keeping operations running smoothly.
- Reduce waste, avoid overstocking, and minimize carrying costs, freeing up cash flow for other business needs.
- Respond quickly to supply disruptions and optimize supply chain management.
- Improve inventory valuation and financial reporting, supporting smarter business decisions.
Work in progress (WIP)
Once you start using your raw materials, they turn into work in progress inventory. Think of WIP as the “in-between” stage. These are products that have started their journey but aren’t ready to hand to customers yet.
Examples of work in progress inventory
- Lotion, socks, and a basket you’re assembling for a holiday gift offering
- Dough that is rising in the proofing drawer
- Skateboard deck and bushings that are waiting for wheels to be screwed in
Managing WIP inventory is essential for keeping your production process running smoothly. When you track components in the production process, you:
- Spot production delays early and address them before they impact customer demand.
- Optimize workflow by identifying where items get stuck or take too long.
- Improve cash flow by reducing the amount of money tied up in unfinished products.
- Increase efficiency by ensuring resources are allocated where they’re needed most.
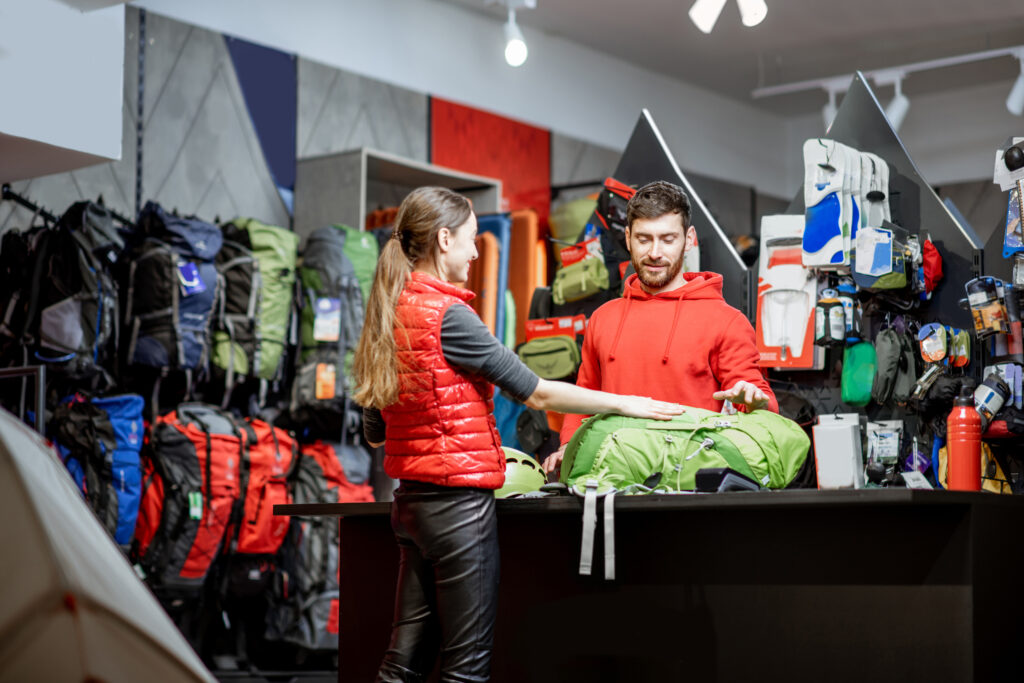
Finished goods
Finished goods are the bread and butter of your store. Once your products are off the production line or show up ready to go on the receiving deck, you have finished goods inventory. These products are fully completed and ready to be sold to your customers.
Examples of finished goods inventory
- Hiking backpack
- Dog shampoo
- Vanilla latte
Finished goods inventory management provides a clear picture of the health of your business. By knowing exactly where all your products are, you:
- Keep popular items in stock to satisfy customer demand and boost sales.
- Avoid excess inventory that takes up space and ties up capital.
- Minimize spoilage and dead stock for perishable goods or seasonal products.
- Balance inventory levels to free up cash while maintaining enough stock to operate efficiently.
Power Up
Have recipes and bundles in your coffee shop? Learn how to track them in your inventory system with our guide.
Maintenance, repair, and overhaul (MRO)
MRO inventory includes all the supplies, tools, and equipment your business needs to keep the doors open. The key to understanding MRO inventory is that they are the products in your store that aren’t sold to customers.
MRO inventory examples
- Cleaning products
- Light bulbs
- Barcode scanner
While these items might not seem as critical as your main products, they play a vital role in supporting your daily operations. By properly managing MRO inventory, you:
- Always have the necessary tools and supplies on hand to avoid interruptions in your workflow.
- Prevent over-purchasing and reduce waste by only stocking what you need.
- Maintain a safe and clean environment with reliable access to cleaning and safety supplies.
- Make sure maintenance and repairs can be handled quickly and efficiently.
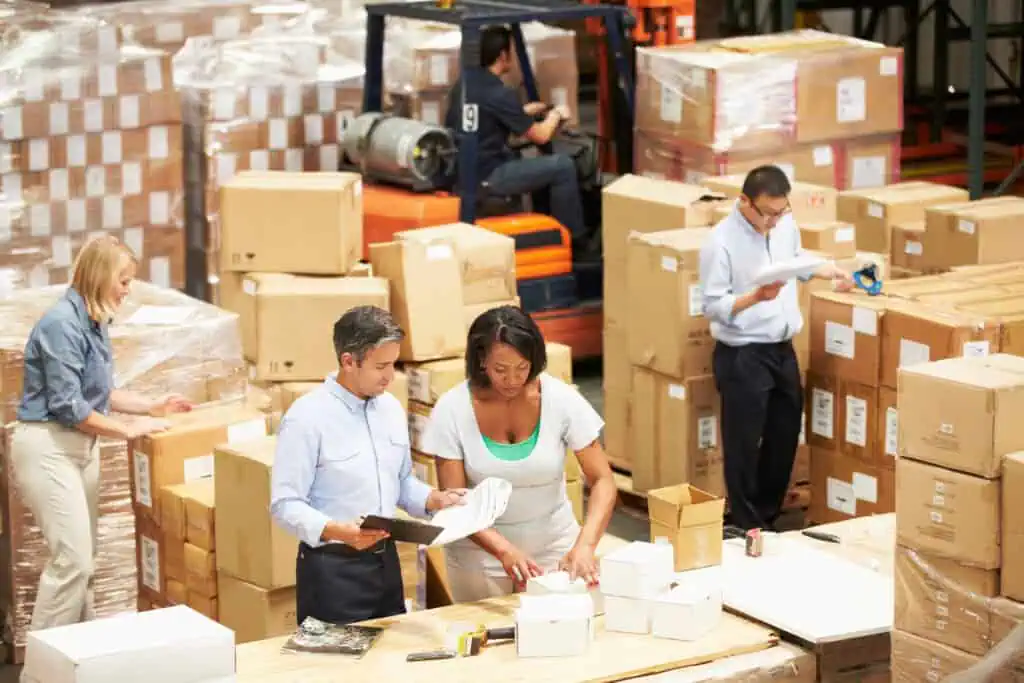
The Newsletter For Small Businesses
Weekly expert insights, industry trends, and inspiring stories designed to help you run your business with confidence.
Inventory Management Strategies For Each Type
Each type of inventory requires a different strategy. While it may seem easier to track components, production, and products the same way, you’ll face higher risk for stockouts, excess inventory, bad stock counts, and incorrect inventory valuation.
Raw materials inventory management
It is essential that you have your raw materials in your inventory management software. Not only does it make reordering and prepping for production easier, but it also allows you to price your productions for how much they’re really worth.
The key to tracking raw materials in your inventory system is to label them as your “input products” and hide them from your sales channels. This keeps them off your e-commerce website so shoppers can’t buy them and off your POS system so your employees have a cleaner catalog to view when checking out customers or helping them find something.
Work in progress inventory management
Bill of materials and recipes
This is where you’ll use bill of material or recipe tracking in your inventory management system. That means your costs and component inventory levels will be calculated in real time at the time of production rather than the time of sale. By linking your raw materials and finished product inventory to your production process, you’ll have greater insight into when you need to reorder components or complete another production run to meet demand.
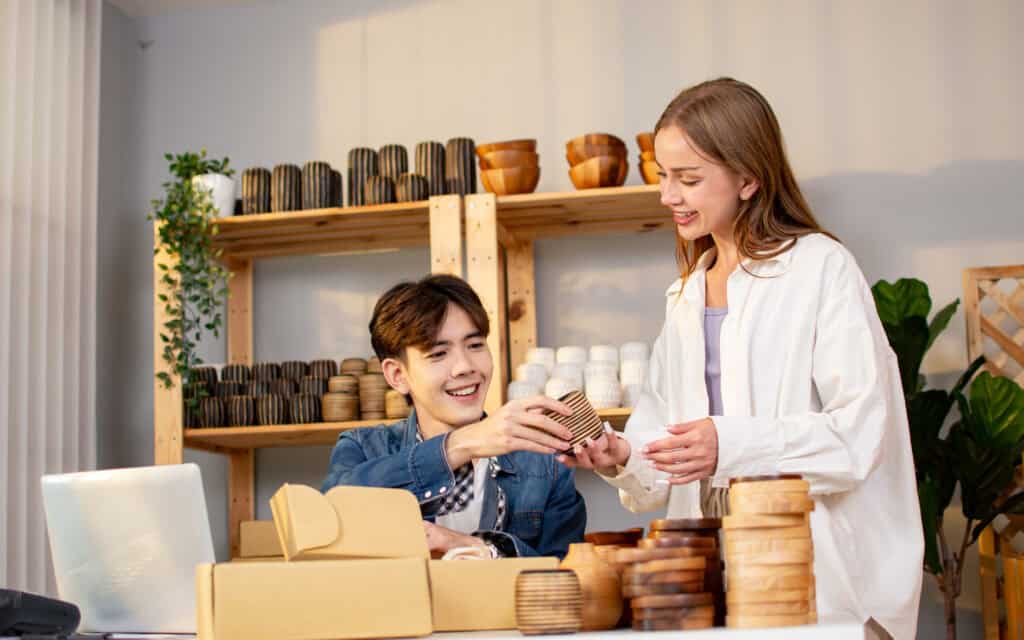
Product bundling
Product bundling is another strategy if you are combining products that sell individually and as part of a new offering. Gift baskets are a perfect example of this. The cheese and crackers that are included in your housewarming gift basket are also for sale apart on your store floor. Bundle inventory management allows you to track stock for a product both individually and in a bundle, so you always have accurate inventory levels and sales data.
Centralize WIP Tracking With Thrive Inventory
Spend more time crafting products you’re passionate about and less time tracking stock levels for your production line. Thrive Inventory deducts and credits the proper quantities for bill of materials, recipes, and bundles.
Finished goods inventory management
These are the products that should be available on your POS and e-commerce sales channel to sell to customers. If you didn’t make these products yourself, you’ll first import them into your inventory management system when you receive them from your vendor. When a customer checks out with a product, stock from your finished goods inventory will be deducted. There are a couple of different ways to manage inventory for finished goods:
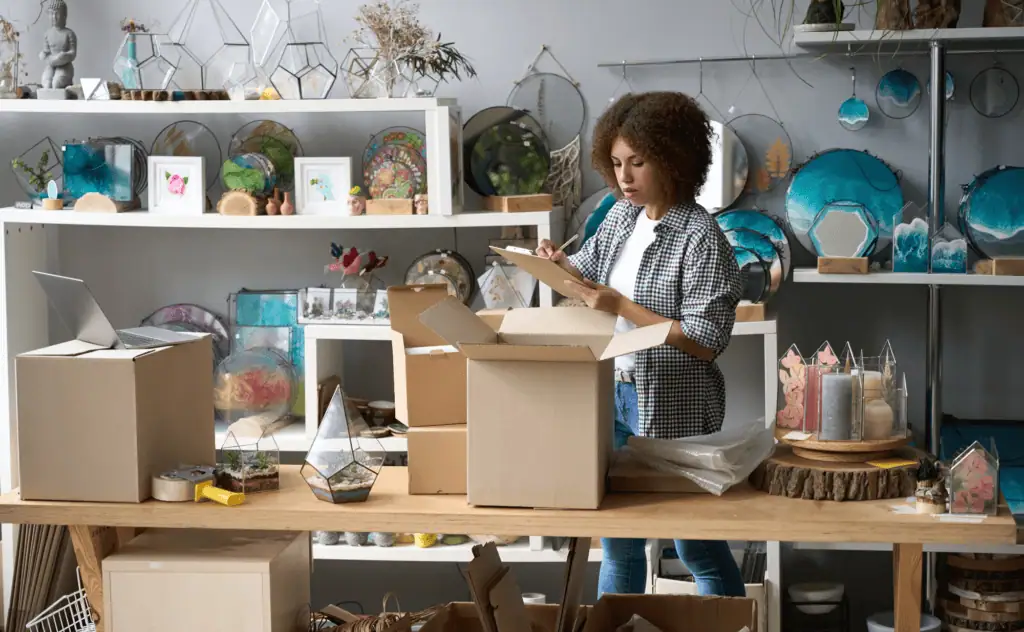
Variants
Color, size, and flavor options are all considered variants and should be accounted for separately. You need to know exactly which variants are performing and which aren’t to dial in your product assortment and also what to put on your next purchase order.
Power Up
Curate your catalog with a product assortment strategy that creates a strong brand image, increases rates, and maximizes profitability. Here are three ways to build a successful product assortment.
Modifiers
Modifiers are finished products that are not available for individual sale but make up a product at checkout. Not to be confused with raw materials or work in progress inventory, modifiers can certainly be homemade but are available to customers at checkout.
Let’s use coffee shop syrups as an example. If you make your syrups in-house, the sugar and extracts would be tracked from raw material to work in progress to finished good inventory. But you don’t sell syrups directly to your customers, so remember to hide it from your sales channel catalog. When a customer orders a vanilla latte at the counter, you’ll deduct inventory for your vanilla syrup modifier.
Centralize Catalog And Inventory Management With Thrive
Experience greater visibility and control of your finished goods inventory with one system that gives you the confidence to run your business.
MRO Inventory
Similar to raw materials, WIPs, and modifiers, you’ll want to hide those products from your sales channels. However, we still recommend keeping them in your inventory management system. That way you know at a glance when to reorder consumables and have a bookkeeping record of how much you’re spending on these products.
Why Knowing Your Inventory Types Drives Success
Effective inventory management doesn’t have to be overwhelming. When you break it down into the four key types, it becomes much easier to see where your money is going and how to optimize your stock. No matter what industry your small business is in, raw materials, WIP, finished goods, and MRO inventory will give you greater control over your business. By taking the time to identify and track these inventory categories, you’re setting your business up for smoother processes and long-term success.
The Only Inventory System That Actually Helps You Run A Healthy Business
Thousands of customers all over the world use Thrive Inventory to run a healthy business.
Thrive Inventory gives you control over all your inventory, sales channels, and metrics, allowing you to make the right decisions at the right time.
Keep Reading
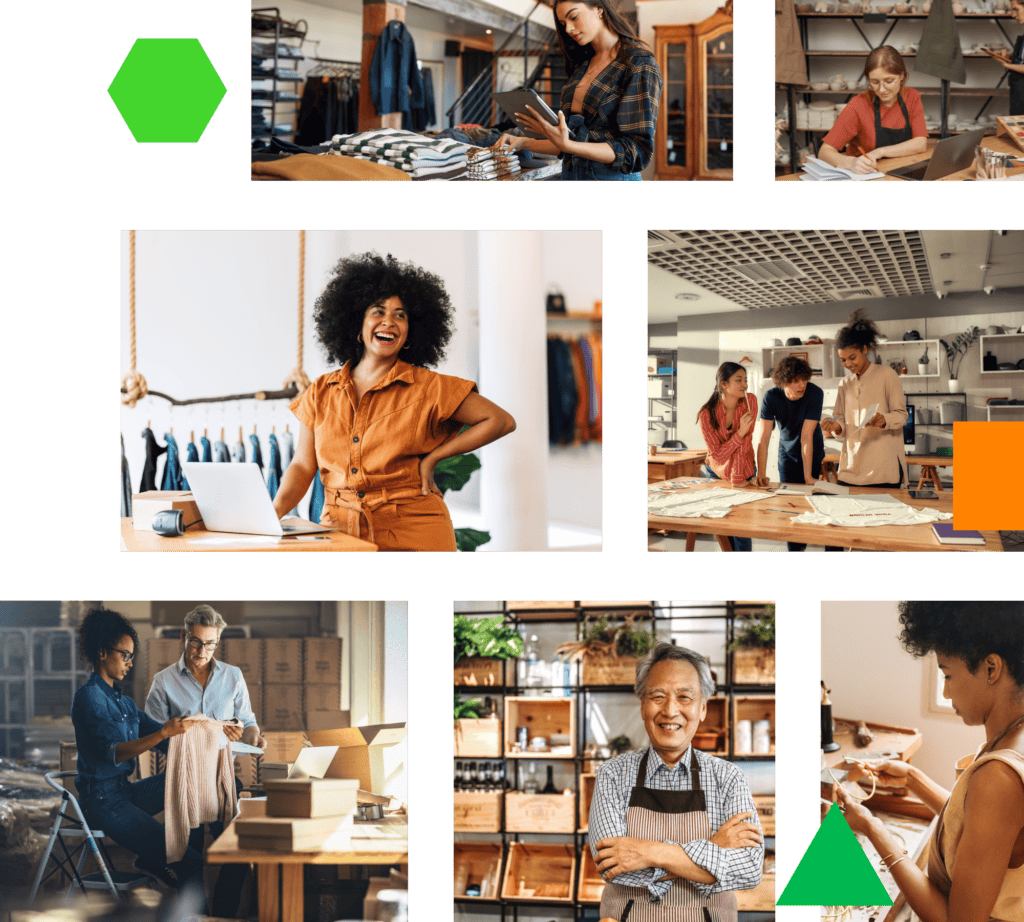
The Newsletter For Small Businesses
Weekly expert insights, industry trends, and inspiring stories designed to help you run your business with confidence.
Try Thrive Inventory For Free
Add Thrive Inventory to your business and maximize your potential. With powerful and easy-to-use products, it’s time to take control of your
business and see what you can do with Thrive.
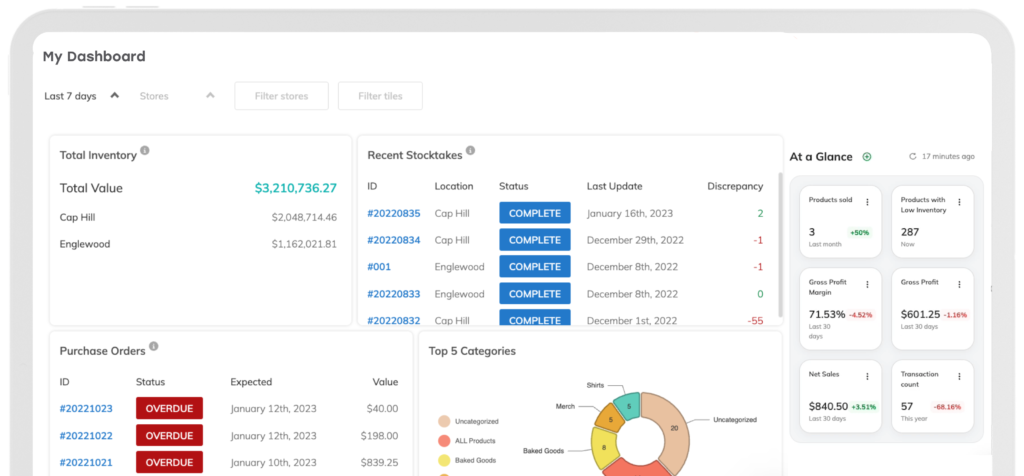